Address: Unit 19, 54 Fairey Rd, South Windsor NSW 2756
Understanding the Importance of Electrical Safety Compliance and Testing
Want to make sure your building is safe and up to code? Whether you operate a manufacturing facility, office complex, or retail space, keeping your electrical systems in good condition is critical for a seamless flow of your business operations. These systems power everything from equipment to lighting, that's why it's essential to make sure they not only work well but also comply with safety standards.
In this blog, we'll explore the key reasons why compliance and testing matter. We'll also delve into the standards for electrical compliance and safety and examine the processes involved in electrical safety testing. Continue reading to learn more.
What does electrical safety compliance and safety testing mean?
Electrical safety compliance involves following established standards, regulations, and guidelines to ensure the safe installation, operation, and maintenance of electrical systems and equipment across various settings, such as homes, workplaces, industries, and public spaces.
On the other hand, electrical compliance testing involves evaluating and verifying the safety of electrical equipment, systems, and installations to ensure they meet established safety standards and regulations. The primary goal of electrical safety testing is to identify and mitigate potential electrical hazards related to reduce the risk of electrical accidents, fires, and other safety incidents.
What is the standard for electrical compliance in Australia?
AS/NZS 3000:2018, also known as the Wiring Rules, is an Australian standard that provides requirements for the design, installation, and maintenance of electrical installations in residential, commercial, and industrial settings. It covers various aspects, including wiring systems, earthing, protection against overcurrent and fault currents, and requirements for specific installations such as switchboards and equipment.
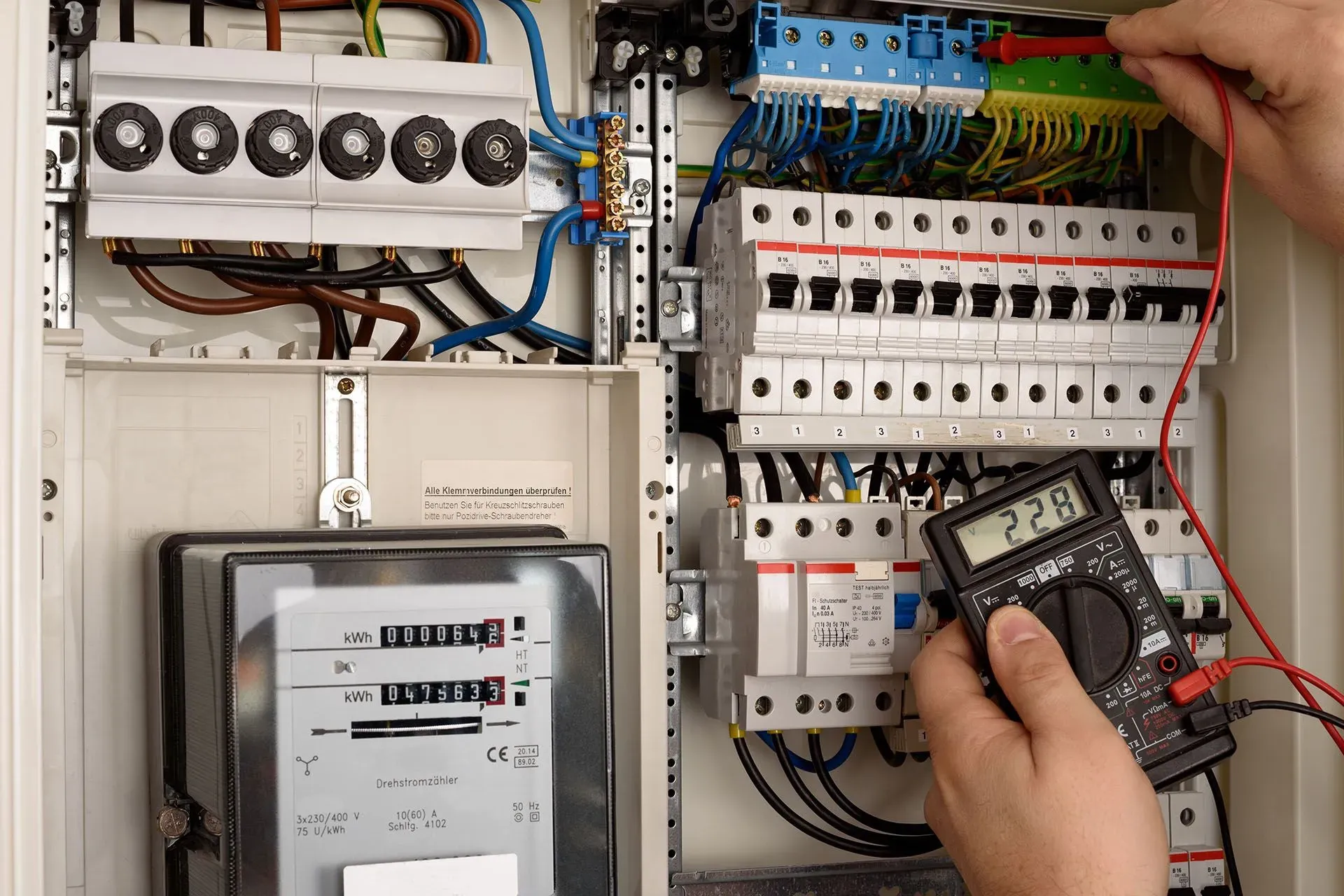
What is the standard for electrical safety testing in Australia?
The AS/NZS 3760 is the primary standard for electrical safety testing of electrical appliances and equipment in Australia. This standard provides guidelines on how a qualified electrician should perform visual inspections, testing, and tagging of electrical appliances to ensure their safe operation. It sets out procedures for testing and tagging to be conducted by competent personnel at specified intervals.
Why is electrical compliance testing important?
Here are key reasons why electrical compliance and testing is important:
Safety
Compliance testing is basically designed for the safety of everyone. It mitigates electrical accidents, fires, and other safety incidents by identifying faults, weaknesses, or potential hazards in electrical systems. Not to mention, it ensures that electrical equipment is properly grounded and insulated, reducing the risk of electric shock to users.
Regulatory Compliance
Not adhering to electrical safety standards can lead to legal consequences, fines, or operational restrictions. Electrical compliance testing and tagging guarantees that you don't face these repercussions by inspecting, testing, and labelling electrical appliances and equipment to make sure that they adhere to the Wiring Rules (AS/NZS 3000).
Risk Mitigation
Beyond legal compliance, routine testing and tagging are crucial in preventing equipment failures, downtime, and unexpected maintenance costs. By performing electrical safety checks, potential issues can be identified and addressed early on before they escalate. This is not only helpful in preventing electrical faults leading to fires or damage to electronic devices but also enhances the reliability and safety of the entire operational infrastructure.
Reliability and Efficiency
Electrical systems need consistent and reliable performance to support the seamless operation of various functions within an organisation. Through electrical testing, businesses can actively ensure the reliability and efficiency of their systems. This not only identifies potential issues but also helps optimise the performance of electrical components. Moreover, adhering to compliance standards improves system predictability, enabling more effective planning and resource management.
Design Improvement
Electrical testing does not only ensure safety but it's also a tool for design improvement. Through systematic testing, organisations can gain valuable insights into the performance of electrical systems and equipment. Identifying areas of improvement in design efficiency and functionality becomes possible, allowing for enhancements that contribute to overall operational effectiveness. This process fosters continuous improvement in the design and functionality of electrical systems.
How often should electrical compliance testing be performed in Australia?
Depending on the type of equipment and its use, the specific intervals for electrical compliance testing can vary.
Portable Appliances
Typically, portable electrical appliances are recommended to undergo an electrical safety check as well as testing and tagging at least every 12 months. However, in some higher-risk environments or for a specific faulty appliance, more frequent testing may be necessary.
Fixed Wiring
Electrical installations in buildings may require periodic inspection and testing at intervals ranging from one to five years. In other cases, more frequent testing may be necessary depending on factors such as the environment and usage.
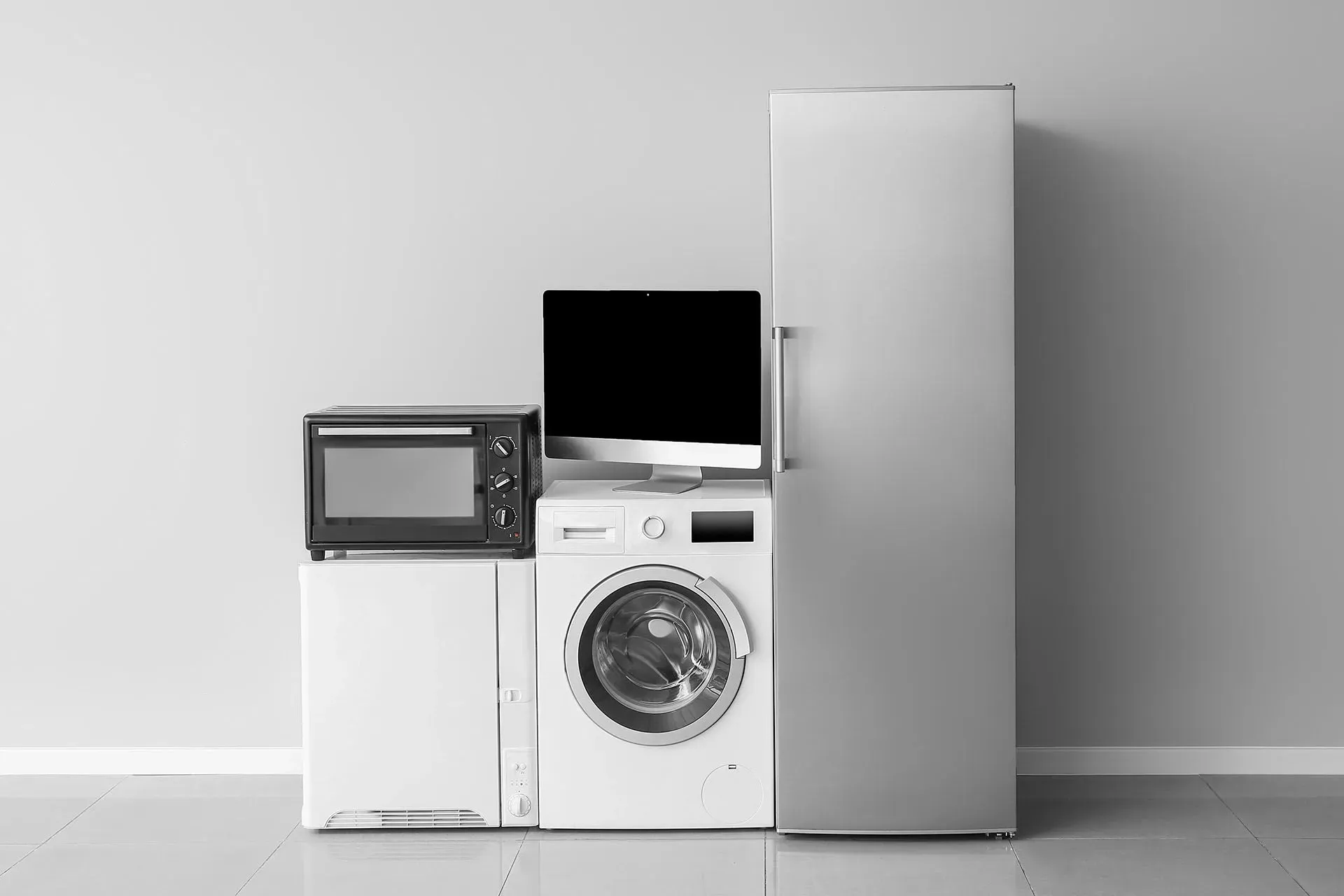
Residual Current Devices (RCDs)
For RCDs, safety switches, or circuit breakers, they may need more frequent electrical safety checks and testing, often every three months, to keep their operations smooth.
What does electrical safety testing cover?
The specifics of electrical safety testing may vary based on the type of equipment and local regulations, but generally, it includes the following:
Testing and Tagging
Testing and tagging involve a combination of visual inspection, electrical testing, and labelling to ensure the safety and compliance of electrical devices. The process is typically carried out at regular intervals to identify any potential issues and confirm that the equipment is safe for use. Key steps in testing and tagging include:
- visual inspection of the appliance to identify any visible signs of damage, wear, or other issues
- electrical safety check using specialised equipment to ensure they meet safety standards, and
- tagging to indicate that it has undergone testing and providing information such as the test date, the name of the tester, and the next scheduled test date.
Earth Continuity Testing
Earth continuity testing or earth bond test, checks how well the grounding system is working. It makes sure there's a good, low-resistance path for any extra electric current in case something goes wrong. This is really important to stop the risk of electric shocks and keep everyone and everything safe. By doing this testing regularly, you can have the peace of mind that electrical systems are safe and that potential risks can be reduced.
Insulation Resistance Testing
An insulation resistance (IR) test measures the total resistance between any two points separated by electrical insulation. This test identifies any potential breakdowns in insulation and determines how effective the dielectric (insulation) is in resisting the flow of electrical current.
Polarity Test
Conducting a polarity test is crucial to verify the correct wiring of electrical equipment like power outlets and extension cords. This test is essential for preventing potential risks and ensuring the safety of both the user and the electrical system.
Functional Testing
Functional testing involves assessing whether the equipment operates as intended and complies with relevant performance standards. It goes beyond checking electrical connections but it is focused on the actual functionality of the device. This type of testing ensures that the equipment performs its designated tasks effectively without compromising safety or efficiency. For appliances, functional testing may include checking the power on/off operation, temperature control, timers and alarms, input and output verification, switches and controls.
RCD (Residual Current Device) Testing
RCD (Residual Current Device) testing involves evaluating the proper functioning of Residual Current Devices, which are safety devices designed to quickly disconnect electrical circuits when they detect imbalances in current. These imbalances could be due to a fault or current leakage to the ground. The testing process for RCDs typically includes a tripping time test, rated residual operating current test, functional test.
Leakage Current Testing
Leakage current testing occurs while the electrical product is in operation. In this process, the electrical device is connected to its operating voltage, and a test is conducted to determine if there is an abnormal flow of electricity or if there is an excessive leakage current flowing through the insulation to the housing.
Portable Appliances Testing
Portable Appliance Testing (PAT) refers to the process of inspecting and testing electrical appliances and equipment to ensure their safety and compliance with electrical standards. This test is essential for maintaining a safe working environment, particularly in workplaces where electrical equipment is frequently moved or connected and disconnected.
Regular Electrical Maintenance
Regular electrical maintenance aims to prevent electrical failures and minimise the risk of electrical accidents by promoting a safe working environment. This process is particularly important in environments where electrical equipment is subjected to harsh conditions or where there is a high potential for electrical hazards.
Electrical Installation Testing
Electrical installation testing involves the evaluation and verification of the electrical systems and wiring within a building or structure to ensure they comply with safety standards and regulations. This type of testing is conducted during the initial installation of electrical systems and can also be performed periodically for existing installations.
Takeaway
Adhering to established safety standards and testing is not only important for the sake of compliance but it is crucial in minimising the risk of accidents, shocks, and injuries. By understanding their importance, businesses can significantly address potential hazards, protect the wellbeing of everyone in the building, and prevent costly damages to equipment and property.
At Ronika, we specialise in providing electrical solutions for building safety and compliance. We offer electrical installations and upgrades as well as workplace testing and tagging to help you achieve electrical safety on your premises. Our team of commercial electricians ensures that your electrical systems not only adhere to the highest safety standards but also enhance the overall efficiency and functionality of your building's electrical systems. Get in touch with us today to request a callback.
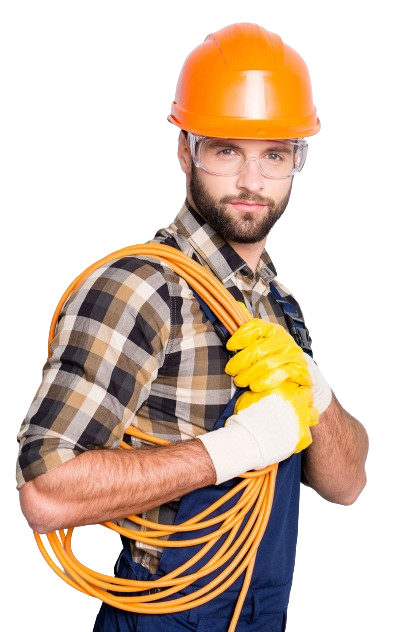